 |
BEFORE |
|
|
Packaging Industry
|
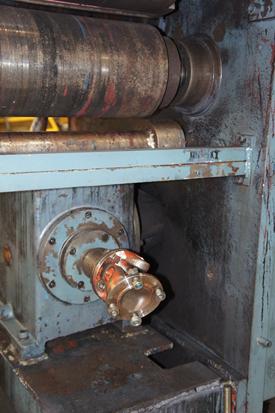 |
AFTER |
|
|
Dry ice blasting has eliminated the cost of replacing the drive belts in the packaging process, as well as the down time required to replace the new belt. Arctic Blast has quickly and easily removed the glue build-up from the belts without damage or wear. Most packaging cardboard boxes are printed with a wax or clay based graphic. As boxes are transported by conveyer rollers, this box coating is rubbed off and transferred onto the rollers. The coating can build up on the rollers to a level where boxes will begin to fall off the conveyor.
|
|
|
Traditional cleaning methods for conveyors requires dismantling every 4 to 10 days and scrubbing with solvents and brushes. The dry ice blasting process thoroughly cleans the wax or clay build up from the rollers while the conveyor is still assembled. Again, cleaning with dry ice blasting reduces the downtime needed for conveyor cleaning, thus increasing line productivity.
All packaged beverage containers have an ink-jet code applied for information transfer and tracking. As with most ink-jet processes, an unwanted over spray occurs on nearby machinery, conveyers, belt drives, and electronics. Consequently, the ink will redeposit onto the package and create an unacceptable finished product. The dry ice blasting process gently removes the ink over-spray and therefore prevents scrap or line shut-down.
|
|